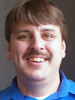
Kevin Gilbert
I was recently helping a colleague find something she had lost on her computer. When I looked over her shoulder, I found every inch of her computer desktop was stuffed with icons. “I know where everything is,” she explained, “I just can’t find my expense report.” I immediately recognized the answer to her problem. She needed 5S.
Lean Manufacturing found tremendous success in the 90’s. Lean Enterprise and Lean Six Sigma gained wide acceptance after the turn of the century. Whether you subscribe to the Lean Philosophy or not, 5S (often called Cando) can improve an office’s productivity, help spot errors, and support quick corrective solutions. 5S comes from 5 Japanese words: Seiri, Seiton, Seison, Seiketsu, and Shitsuke. 5S is simple and easy to follow practices that can have a positive impact on every day activities.
The following explains how to implement 5S:
- Sort (Clean up): Remove everything from your work area and computer desktop that doesn’t apply to the task at hand. Removing clutter can help you focus and allows errors to become obvious. Cleaning up before you start will save time you normally might spend searching for things you need.
- Set in order (Prepare the tools): Make sure you have any necessary software, websites, and office tools within arm’s reach. For example, if you need binders and 3-hole punches, gather them before you begin. Another example, you don’t want to be in the middle of a task and run out of staples – be disciplined and keep your office supplies stocked.
- Shine: They say cleanliness is next to godliness. More specific to the task at hand, cleanliness aids focus, reduces distraction, and can keep you from becoming ill. Sweep out those crumbs from under your keyboard. Wipe off the coffee circles from your coffee cup. Wash your hands often to prevent the spread of germs. Finally, keep white boards and bulletin boards clean and clutter free. Make your surroundings shine.
- Standards: Suggest creating a standards program across your office for the implementation of 5S best practices. For example, how long will something be posted on the bulletin board before it is taken down? Who should be responsible for erasing white boards in meeting rooms? If your organization has a Clean Desk Policy, how is it followed and enforced? Establish rules concerning starting meetings late or having a meeting run too long. Suggest incentives and rewards for following the standards. Perform inspections to make sure standards are being followed. The implementation of 5S Standards supports the ISO 9000’s process and control requirement.
- Sustain: For many, 5S is an office cultural change and will require efforts for sustainability. Sustainability means enforcement and continual improvement. A seemingly minor issue (such as, is a 3-hole punch available when needed) may seem minor at first, until it is understood how much time is wasted by employees searching for office supplies, waiting for necessary software installations, or meetings starting late. Offices should have a regular review for the placement of printers, copiers, supply closets, and other office needs to assure additional burdens aren’t unnecessarily being placed on the daily efforts of employees. For example, does it make sense to schedule the quarterly copier maintenance in the middle of a large effort when the copier is needed the most? Continual improvement efforts should aim at finding the root causes for office problems and then improving the situation.
The purpose of 5S is to encourage office employees to develop their work environments in ways that reduce waste, increase time efficiency and optimize equipment use supplies.
When used correctly, 5S can increase office productivity. An office that gives employees a say on how to obtain better focus, fewer errors, and higher productivity is an office that will have higher morale. Whether your office is following a Lean philosophy or not, 5S can help.
Resources:
Image Courtesy: http://www.qualitycoach.net/data/i2/5Senna1.jpg
About the Author:
Kevin Gilbert is the Technology Manager at SIGMA Marketing Group. Kevin headed the data center virtualization project for four years and is a VMWare Certified Professional (VCP). Connect with Kevin on .
Related Articles: